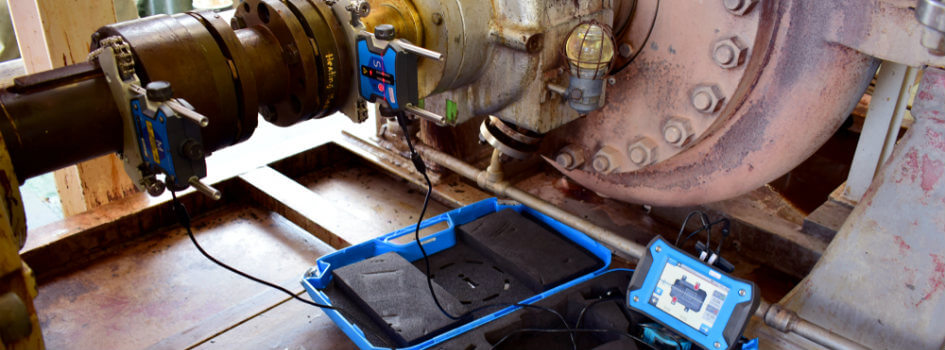
5 Tips to Prevent Rotating Equipment Problems from Happening
Your essential rotating machinery (like motors, generators, and centrifugal pumps) need routine maintenance to operate at peak performance. As you know if you’ve already experienced a serious mechanical failure, a serious mechanical failure can only mean two things: expensive machine damage and costly downtime.
Here are five tips you can implement to lessen the cost and frequency of preventable equipment break-downs.
1. Keep Good Maintenance Records
Recordkeeping should be an emphasis of every part of an industrial maintenance plan, but it is especially important for rotating equipment. There are lots of data analytics tools now available to help you track equipment performance and spot signs of wear. Sometimes a small anomaly identified by your rotating equipment condition monitoring can provide a warning that it’s time to conduct a more detailed investigation.
2. Address Problems Early and Quickly
There’s no good time to fix equipment. One of the best ways to save costs and avoid downtime is to fix performance issues as soon as possible. Allowing a misaligned shaft or failing bushing to remain in place can lead to far more significant and expensive failures.
Among other things, addressing problems early on ensures that maintenance can be done according to the business’s schedule, rather than according to a schedule dictated by broken parts. If your rotating equipment vibration analysis shows that a critical piece of machinery needs maintenance, don’t put it off.
3. Keep a Clean Shop
Inspecting a facility for faults is much easier if it is kept clean. This is especially true with rotating equipment, which also runs more efficiently if it is free of dirt and other contaminants. Routine cleaning has an added benefit of providing another opportunity for problems to be spotted beyond using equipment and pump condition monitoring systems.
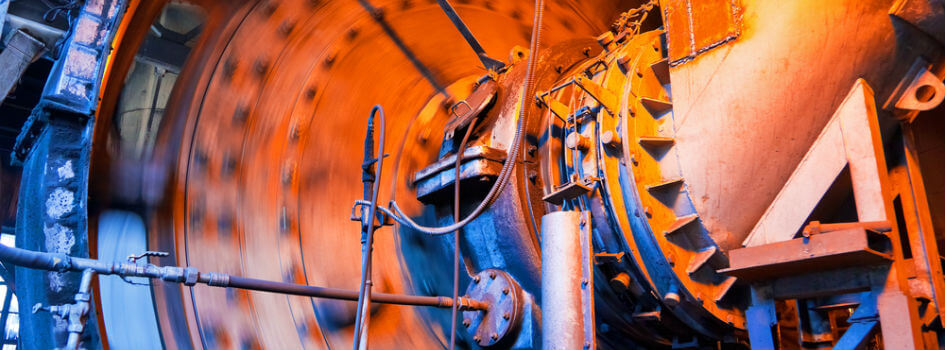
4. Trust Your Senses
In our era of advanced electronic sensors, it can be easy to dismiss the power of human senses. People who regularly work around rotating machinery may sense something is wrong by the way a machine sounds, smells or feels. An unusual vibration could indicate a misalignment that needs to be corrected. A sound might indicate that a part is insufficiently lubricated. All this sensory information is important and worth further investigation.
5. Make Safety the Top Priority
Anyone who will perform inspections or maintenance work on rotating equipment needs to be trained in correct safety protocols. If the business does not have the internal resources to develop its own safety procedures for maintaining equipment, it should source industrial safety services from a third party.
DXP Enterprises provides a complete range of technical services for clients across multiple industrial markets. We help rotating equipment operators assess their maintenance needs, train employees, and optimize their processes to improve performance and reduce downtime.
To learn more about what DXP can do for your business give us a call today or schedule a time for us to contact you.