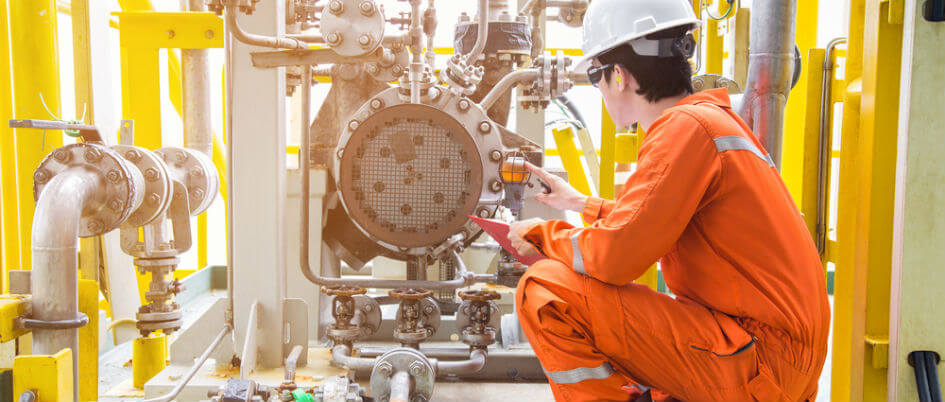
Pump Monitoring of Centrifugal Pumps for Decreased Downtime
Centrifugal pumps form an integral part of many industrial processes. These machines are commonly used in the chemical transportation and processing industry to channel process fluids through various manufacturing systems.
Like any other machine, centrifugal pumps require routine monitoring to assess their operational state and allow operators to promptly institute cost-saving maintenance activities.
Importance of Pump Monitoring
Prolonging the lifespan of mechanical pump systems while maximizing process efficiency is very important to plant operators. To effectively maintain centrifugal systems, the use of remote pump monitoring systems and predictive maintenance is of utmost importance.
Failure to allocate the necessary resources to equipment monitoring can eventually lead to pump breakdown, costly downtime, and even hazardous working conditions. Additionally, unmitigated long-term wear/damage from lack of scheduled maintenance will drive up operational budgets as replacing faulty parts are generally costly endeavors.
To avoid the above pitfalls, industrial equipment operators must ensure they implement well-coordinated equipment condition monitoring systems. The measurement of variables like the flow rate, fluid levels, vibration, and temperature, will facilitate the early detection of underlying pump problems.
4 Pump Monitoring Methods
Different pump operators use varied approaches to remote pump monitoring depending on the type of centrifugal system they operate. Some of the most effective ways to conduct automated pump monitoring include:
- Head-flow method
- Thermodynamic method
- Shut-off head method
- Pump vibration method
The remote monitoring techniques listed above detect and analyze physical variables including temperature, pressure, and vibrations to facilitate predictive maintenance of associated centrifugal pump systems.
Head-flow Method
This is the most useful pump monitoring system as it not only detects pump deterioration, it also identifies changes in the resistance to fluid flow within the pump system. Test gauges are used to determine differential pressures across the orifice plate of the pump being analyzed. Once baseline pressure parameters are collected, regular checks will allow rapid detections of any alterations from the previously recorded data. Information gotten by this method will help operators predict possible machinery failure and intervene early.
Thermodynamic Method
Measuring the temperature patterns of fluid flowing through a centrifugal pump is another effective method of monitoring. As a pump undergoes wear and becomes less efficient, there is a gradual rise in the thermal conditions within its housing. However, the temperature changes are usually subtle and require very sensitive devices to detect the changes.
Normal sources of thermal change such as fluid recirculation at pump inlets and outlets must be disregarded to obtain an accurate picture of pump temperatures. Data regarding inlet temperature, the differential temperature, and the head can be used to calculate overall system efficiency. Plotting graphs of efficiency versus head over time will provide crucial information on significant changes in temperature indicative of machinery wear and tear.
Shut-off Head Method
The shut-off head method is best suitable for predictive maintenance in pump systems that allow head measurements at zero flow. This method is not recommended in high-energy, high specific speed pumping systems as they pose a significant risk of explosion when operated at zero flow.
Shut-off head monitoring is relatively simple and requires the inspector to measure the suction and discharge pressures for no longer than 30 seconds with fully shut-off discharge valves. Pump fluid temperatures are also obtained separately to determine density. A plotted head-flow curve shifting towards the zero axis is indicative of wear to the outer diameters of the pump vanes while a steep curve indicates wear of the inner seal ring.
Pump Vibration Method
All rotating equipment (pumps included) has unique vibrating characteristics that change with the onset of wear in their dynamic or static parts. Changes in the vibration patterns of centrifugal pumps can predict subtle component damage undetectable by visual or auditory inspection. For example, a failing bearing or broken impeller will lead to increased vibration during pump operation.
Remote pump vibration monitoring sensors will provide real-time frequency readings to a remote monitoring system for collation, analysis, and interpretation without requiring human effort as other methods described. DXP offers wireless, cloud-connected, proactive machine health monitoring systems for round the clock analysis of thermal and vibration data from your machinery allowing timely decision making on maintenance.
When Does My Centrifugal Pump Need an Overhaul?
While routine pump monitoring will detect all machine-related wear regardless of the degree of severity, it won’t determine how to deploy your budget of equipment repairs/ replacements. The decision on when to intervene should be taken to maximize outcomes at every point.
A cost-benefit analysis should be conducted to determine which maintenance activities to prioritize. For example, machinery damage driving up utility costs or slowing down production should take precedence over other minor signs of wear. Costs savings in these scenarios are among the main benefits of condition monitoring.
DXP Has the Perfect Remote Pump Monitoring System for You
At DXP Enterprises, we offer custom-built solutions for a wide range of industries. We also offer our clients smart remote monitoring technology. For companies seeking to make their production processes more effective, DXP is the right fit.
Contact us online today to learn more about our state of the art remote pump monitoring systems.