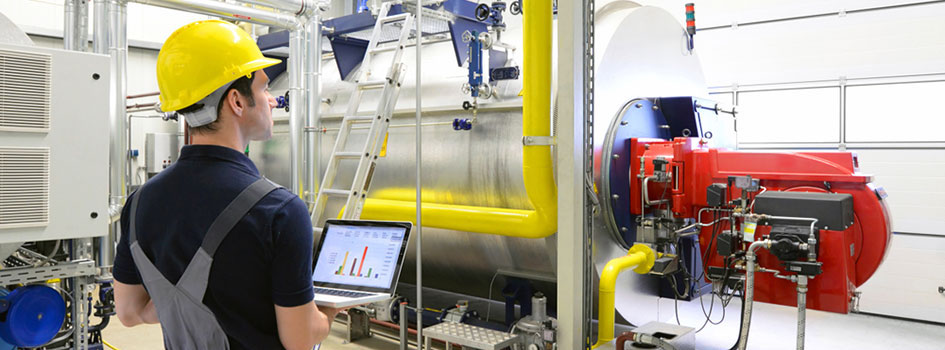
What Is Factory Acceptance Testing (FAT) & How Does It Work?
New equipment can be incredibly complex with countless opportunities for error. Fortunately, Original Equipment Manufacturers know better than to hope for the best – they plan for the best.
By testing the equipment or components before the customer receives them, DXP can increase the odds that new installations will perform as expected. Planning, documenting, and testing the equipment before delivery ensures the product consistently meets the customer’s expectations.
DXP makes this possible with Factory Acceptance Testing.
What Is Factory Acceptance Testing?
Factory Acceptance Testing (FAT) is a process within the manufacturing and quality assurance phase of industrial equipment or systems. It involves a series of tests and inspections conducted by the manufacturer or supplier to ensure that the product meets the specified requirements, design criteria, and functionality before it is delivered to the customer.
Purpose of a Factory Acceptance Test
The Factory Acceptance Test is valuable for both end-users and manufacturers. It ensures the new equipment meets all agreed-upon specifications, preventing issues at the client’s site. Fixing manufacturing issues before the equipment leaves the manufacturer helps control the project’s timeline and budget. The FAT is a cost-effective solution, preferred over addressing issues after deployment.
Is a Factory Acceptance Test Different from a Site Acceptance Test?
A Factory Acceptance Test is a test that runs on the equipment or components before they are delivered to their intended destination. While FATs can use simulations to demonstrate how the equipment will function in its future operating environment, it may be difficult to mimic the actual operating conditions.
A Site Acceptance Test (SAT) can be conducted after the FAT has taken place and the system has been delivered and installed. This is the only way to determine whether a piece of new equipment will function as needed.
Factory Acceptance Test Protocol
Here are three FAT protocols that can be used to guide a successful test.
Step 1. FAT Planning
Objective: The first step in a Factory Acceptance Test is planning. This planning happens when the manufacturer or OEM outlines what the FAT will include during the bid phase of the customer’s order. The plan, which is put into writing, covers all customer specifications, standards, and drawings.
By defining the scope of the FAT, we ensure that the equipment provided is acceptable and credible. This plan is shared with the customer from the beginning to make sure it aligns with their expectations and requirements.
Step 2. Engineering and Materials Documentation
Objective: This step involves gathering and documenting all engineering and materials information related to the equipment or system being tested.
A complete set of reference documents will be assembled before the FAT testing. These documents will include, but not be limited to:
- Customer scope and specifications
- Drawings (GA, P&ID, etc.)
- Data Sheets
- ITP (Inspection Test Plan)
- Applicable Codes / References
- Checklists and Procedures specific to the FAT
- Calibrations and Certifications as required by the contract
Along with the documents listed above, other manufacturing documents are reviewed by the manufacturer / OEM to verify that the equipment supplied meets the design drawings and the customer’s requirements before the FAT. Any instrumentation used to record data during the test will be verified within the calibration date as required by the manufacturer or customer specifications before the test.
Step 3. Testing
Objective: The final step is the actual testing phase, where the equipment or system is subjected to various tests and inspections to verify its compliance with specified requirements.
During the Factory Acceptance Test, the following should be accomplished:
- Following and referencing the ITP and FAT Procedures listed above.
- Raw data will be taken, recorded, and submitted to the customer.
- GA, P&ID, and electrical drawings will be reviewed with the customer or their representative.
- Any NDE, Coating, Transportation, or Storage Procedures will be reviewed.
- Job-specific requirements as referenced in the customer specifications.
By following these three steps, the Factory Acceptance Test Protocol aims to systematically plan, document, and execute a comprehensive testing process to verify the quality and functionality of industrial equipment or systems before they are delivered to the customer.
DXP Is a Trusted Industrial Supplier of Quality Process Equipment
If you are a manufacturer looking for industrial equipment supplies, let our globally trusted experts assist you. DXP is one of the world’s leading global MRO industrial supply companies.