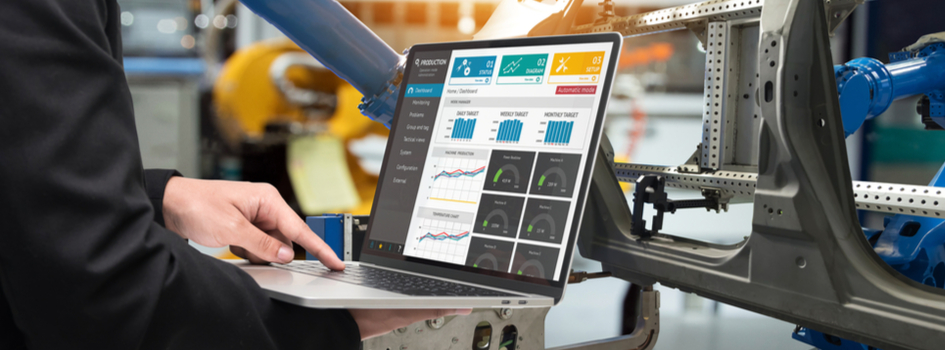
10 KPIs Every Industrial Company Needs to Track
Manufacturers and proprietors of industrial companies are in an industry of non-stop growth. Sometimes, this growth can seem immeasurable because of the numerous metrics involved with manufacturing.
Essential Industrial KPIs to Track
If you want to scale your business, gathering and analyzing data is necessary. Reviewing your metrics can help you identify the weak points in your production or operation processes, allowing you to constantly improve and polish your business practices.
This article examines the top KPIs manufacturing leaders use to maintain and streamline their business processes.
1. Yield
Yield is arguably one of the most important of the industrial KPIs. It’s certainly one that most people in the industry are already familiar with. Yield can be divided into two different metrics: Overall Yield and First Pass Yield.
Overall Yield is the percentage of products produced that may or may not require more work to meet quality and compliance standards.
First Pass Yield, on the other hand, is the percentage of products that were manufactured perfectly to specifications without any re-work. First Pass Yield is calculated by the number of units coming out of the process divided by the number of units put into the process over a specific period.
2. Throughput
Throughput is one of the most critical metrics in manufacturing. Other industrial KPIs carry weight, but throughput is one of the golden standards. Throughput weighs the average number of units produced on a machine over a specific period, such as units per minute.
When your throughput decreases, the problem stems from the machine or on the line. Conversely, increased throughput comes from lean processes, automated equipment, or eliminated downtime.
3. Overall Operating Efficiency
Widely recognized as OOE, Overall Operating Efficiency is an analysis of productivity and efficiency. OOE includes standard time as well as off standard time. The objective is to maximize this metric so that employees contribute value to the company for the better part of the time they’re on the clock.
4. Overall Equipment Effectiveness
Overall Equipment Effectiveness or OEE is a metric used to measure the overall effectiveness of a particular piece of production equipment or the entire line. OEE tracks the quality, speed, and downtime of your operations.
5. On-Time Project Delivery
As the name suggests, this metric is based on the percentage of orders successfully shipped in full and measured against all orders according to schedule. The metric shows how likely you are to serve your customers seamlessly. For this metric, 100% should always be the goal.
6. Total Cycle Time
Cycle time is defined as the total time from the beginning of the process to the end. The amount of time an item spends inside the manufacturing system between the order and completion is the “total manufacturing cycle time.” Decreasing this time can result in lower operational costs and increased flexibility.
7. Capacity Utilization
This metric defines how much of the total output capacity is being used at any given time. Capacity utilization is displayed as a percentage of total possible output, which allows you to look at what — or who — isn’t being efficient. When your entire facility is working at full capacity, your capacity utilization is at 100%.
8. Inventory Accuracy
Inaccurate inventory reports cause a loss in revenue, increased downtime, and extended project delivery. Inventory management is important because it can delay production or slow down the line, costing money. Ensuring that all inventory reports are correct will save manufacturers energy, time, and money that would’ve been spent unnecessarily.
9. Machine Downtime
Machine downtime is a metric that’s a component of OEE. Still, it’s so important that it is worth knowing the measurement itself. Machine downtime can include scheduled maintenance that renders the machines inoperable, setup, machine changeover, or any time the machines in your facility aren’t running.
10. Repair Spend
Repairs are sometimes unavoidable, and they are almost always costly. However, it is crucial to conduct due diligence to ensure your machines and tools are being appropriately used to prevent wear and tear. Machines put under unnecessary stress by employees will need repair before they would’ve had they been used properly.
SmartSource Key Performance Indicator Reporting From DXP
DXP’s SmartSource KPI dashboard reporting provides business owners and industrial companies with the measurements of on-time delivery, stock item fill rate, vendor invoices, repair spend, stock spend, and many more reports that make it easy to keep your eye on the important industrial KPIs that influence your organization’s success.
The simple, user-focused design grants proprietors the power to see all of the metrics they need, with organized data that they can use to improve their business processes. SmartSource by DXP is a dynamic software that can transform how business owners review their KPIs.