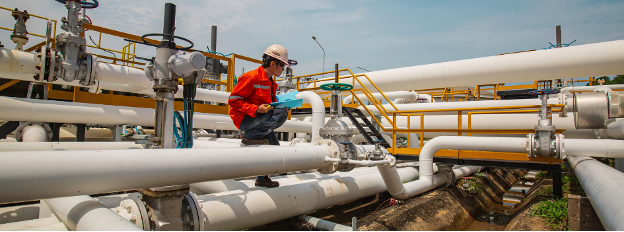
Identifying Common Pump Performance Issues
Even the most reliable rotating equipment can experience performance issues that can disrupt operations, lead to costly downtime, and necessitate repairs. Troubleshooting common pump performance issues is crucial for maintaining efficiency and minimizing disruptions.
The Consequences of Neglecting Pump Problems
Ignoring common pump performance issues can lead to severe consequences that impact both your operations and bottom line. Without proper maintenance and timely troubleshooting, minor problems can escalate into major failures. Unaddressed issues can cause complete pump breakdowns, resulting in costly downtime and expensive repairs.
Furthermore, inefficient pump operation can lead to increased energy consumption, driving up operational costs. In the worst-case scenario, neglected pump problems can pose safety risks to personnel and lead to environmental hazards due to leaks and spills. Proactive pump health monitoring and prompt attention to performance issues are essential to ensure the longevity and reliability of your pumps.
1. Insufficient Flow Rate
Problem:
An insufficient flow rate occurs when a pump is unable to deliver the expected volume of fluid.
Causes:
- Clogged or Blocked Pipes: Debris or sediment can obstruct the flow.
- Worn Impeller: Over time, the impeller can wear out, reducing its efficiency.
- Incorrect Pump Sizing: A pump that is too small for the application will struggle to meet demand.
Solutions:
- Inspect and Clean Pipes: Regular pump tests and maintenance to clear blockages can restore proper flow.
- Replace Impeller: If wear is detected, replacing the impeller can improve performance.
- Reevaluate Pump Sizing: Ensure the pump is correctly sized for the application. Consulting with a professional can help determine the appropriate pump capacity.
2. Excessive Noise and Vibration
Problem:
Excessive noise and vibration are not only disruptive but can also indicate underlying issues that may damage the pump.
Causes:
- Misalignment: Improper alignment of the pump and motor can cause vibrations.
- Cavitation: When vapor bubbles form and collapse within the pump, it can lead to noise and damage.
- Worn Bearings: Bearings that are worn out can cause excessive noise and vibration.
Solutions:
- Check Alignment: Regularly check and correct the alignment of the pump and motor.
- Address Cavitation: Ensure the pump is operating within its recommended parameters and check for blockages or design issues causing cavitation.
- Replace Bearings: Regularly inspect bearings and replace them if wear is detected.
Learn More About Vibration Monitoring.
3. Overheating
Problem:
Overheating can lead to pump failure and is often a sign of an underlying issue.
Causes:
- Insufficient Cooling: Inadequate cooling can cause the pump to overheat.
- High Operating Temperatures: Operating the pump at temperatures higher than its design limits.
- Mechanical Friction: Excessive friction from worn parts can generate heat.
Solutions:
- Improve Cooling: Ensure the pump’s cooling system is functioning correctly and efficiently.
- Operate Within Limits: Make sure the pump operates within its specified temperature range.
- Reduce Friction: Regularly inspect and lubricate moving parts to minimize friction.
4. Loss of Prime
Problem:
A pump losing its prime can lead to a complete stoppage of fluid movement.
Causes:
- Air Leaks: Leaks in the suction line can introduce air, causing the pump to lose prime.
- Improper Priming: Not priming the pump correctly before operation.
- Low Fluid Levels: Insufficient fluid in the supply tank.
Solutions:
- Seal Leaks: Inspect and seal any leaks in the suction line.
- Proper Priming: Follow the manufacturer’s instructions for correctly priming the pump.
- Maintain Fluid Levels: Ensure the supply tank is adequately filled to prevent air from entering the pump.
5. Seal Leaks
Problem:
Leaks around the pump seals can lead to fluid loss and contamination of the surrounding environment.
Causes:
- Worn Seals: Over time, seals can wear out and fail.
- Improper Installation: Incorrect installation of seals can lead to leaks.
- Excessive Pressure: Operating the pump at pressures higher than the seals can handle.
Solutions:
- Replace Seals: Regularly inspect and replace worn seals.
- Correct Installation: Ensure seals are installed correctly according to the manufacturer’s guidelines.
- Manage Pressure: Operate the pump within its designated pressure range to avoid stressing the seals.
Learn More About Leaking Pump Seals.
Keep Your Pumps Running Smoothly with DXP
At DXP, our team of experts is here to help you troubleshoot and resolve any pump performance issues you may encounter. From providing high-quality replacement parts to offering professional pump predictive maintenance and repair services, we ensure your pumps operate efficiently and reliably.
Ready to learn more about our comprehensive pump solutions? Let’s talk.