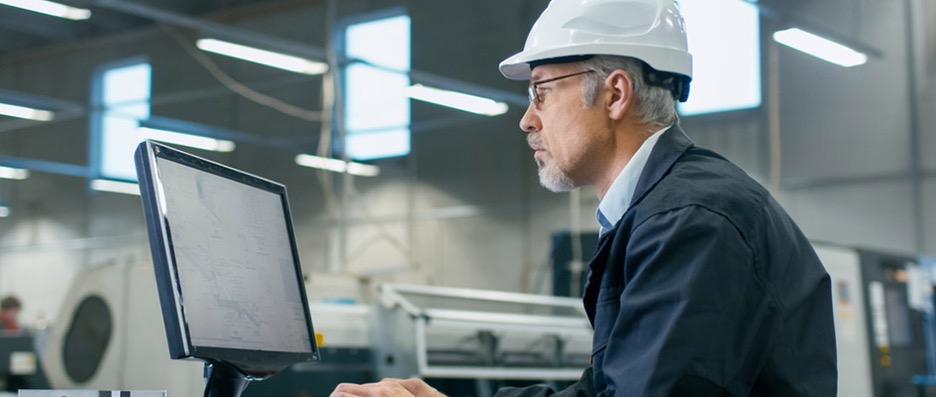
What is an Equipment Health Monitoring Device?
As industries continue to embrace digital transformation, equipment health monitoring devices will play a big role in shaping the future of maintenance and asset management. Keep reading to learn more.
Understanding Equipment Health Monitoring Devices
Equipment Health Monitoring (EHM) is a sophisticated tool designed to oversee the condition of machinery and equipment in real time or at regular intervals. EHM devices utilize a combination of sensors, data analytics, and connectivity technologies to gather data on various parameters such as temperature, vibration, pressure, and more.
The primary objective of EHM is to detect anomalies, predict potential failures, and enable proactive maintenance interventions before critical issues arise.
How Do Equipment Health Monitoring Devices Work?
Asset monitoring devices provide a multi-faceted approach to overseeing equipment health. Here’s how they work:
- Sensor Integration: These systems are equipped with an array of sensors strategically placed on the equipment to capture relevant data points.
- Data Acquisition: These devices collect data continuously or periodically from the sensors regarding different parameters like temperature, vibration, fluid levels, etc.
- Data Analysis: The collected data is then analyzed using advanced algorithms and machine learning techniques to identify patterns, trends, and deviations from normal operating conditions.
- Condition Assessment: Based on the analysis, EHM devices assess the condition of the equipment, flagging any abnormalities or potential issues.
- Alerts and Notifications: When anomalies are detected, the system can generate alerts or notifications, enabling maintenance teams to take timely corrective actions.
- Predictive Maintenance: EHM can predict potential failures by analyzing historical data and patterns — allowing for proactive maintenance scheduling and minimizing unplanned downtime.
Applications Across Industries
Several types of industrial equipment can benefit from condition monitoring — everything from manufacturing machinery to infrastructure and healthcare equipment.
Rotating Equipment
Rotating equipment such as pumps, motors, turbines, and compressors are critical components in various industrial processes. Condition monitoring helps detect issues like misalignment, imbalance, bearing wear, and lubrication problems, ensuring smooth operation and preventing costly downtime.
Power Generation Equipment
Power plants rely heavily on equipment like boilers, generators, and transformers. Continuous monitoring of parameters such as temperature, vibration, and oil conditions helps anticipate potential failures, enabling proactive maintenance and enhancing operational reliability.
Manufacturing Machinery
Equipment used in manufacturing processes, including CNC machines, presses, and conveyors, are susceptible to wear and tear over time. Predictive monitoring allows manufacturers to identify degradation in components like gears, belts, and bearings, optimizing maintenance schedules and minimizing production disruptions.
HVAC Systems
Heating, ventilation, and air conditioning systems are vital for maintaining comfortable and safe indoor environments. Paying attention to airflow, temperature, and refrigerant levels ensures efficient operation, reduces energy consumption, and prevents unexpected breakdowns — which are very important in commercial and industrial settings.
Transportation Assets
Industries reliant on fleets of vehicles or heavy equipment (such as mining, construction, and transportation) benefit from condition and vibration monitoring systems to keep their assets running smoothly. Monitoring engine performance, tire condition, and hydraulic systems helps maximize uptime, improve safety, and extend equipment lifespan.
Pipelines and Oil & Gas Infrastructure
Pipelines, refineries, and offshore platforms require continuous supervision to ensure operational integrity and safety. Monitoring techniques such as corrosion monitoring, leak detection, and pressure monitoring help mitigate risks, prevent environmental disasters, and maintain regulatory compliance.
Aerospace and Defense Systems
Aircraft, satellites, and military equipment demand rigorous monitoring to ensure mission success and personnel safety. Remote machine monitoring helps detect anomalies in engines, avionics, and structural components, allowing timely maintenance and enhancing operational readiness.
Benefits of Equipment Health Monitoring
The adoption of machinery health monitoring offers countless benefits to businesses:
- Improved Equipment Reliability: EHM devices enable early detection of faults, preventing equipment breakdowns and minimizing unplanned downtime.
- Cost Savings: Proactive maintenance based on insights reduces repair costs, extends equipment lifespan, and optimizes maintenance schedules, resulting in significant cost savings.
- Enhanced Safety: By identifying potential safety hazards in advance, EHM helps mitigate risks, ensuring a safer working environment for personnel.
- Increased Operational Efficiency: Industrial machine health and asset monitoring optimizes equipment performance, improving productivity and operational efficiency.
- Data-Driven Decision Making: The wealth of data provided by EHM empowers organizations to make informed decisions regarding equipment maintenance, investments, and resource allocation.
Equipment Health Monitoring FAQs
Is condition monitoring only beneficial for older equipment, or can it also be applied to new machinery?
Condition monitoring is valuable for both new and older equipment. For new machinery, it helps establish baseline performance metrics and detect any early signs of defects or assembly errors. For older equipment, it aids in identifying age-related degradation and wear.
Can condition monitoring detect all potential equipment failures?
While equipment health monitoring can detect many types of equipment faults, it may not identify every possible failure mode. However, by combining multiple monitoring techniques and data analysis, organizations can effectively detect and address various issues.
How do I justify the investment in condition monitoring?
The potential cost savings from reduced downtime, decreased maintenance costs, improved productivity, and enhanced asset performance can help demonstrate the return on investment (ROI) of implementing remote monitoring.
Explore DXP’s Equipment Health Monitoring Solutions
Ready for enhanced reliability, efficiency, and profitability? Visit DXP’s website now to discover how our remote pump monitoring systems can transform your operations and drive unparalleled efficiency and reliability. Don’t wait until it’s too late – invest in the future of your business today with DXP.