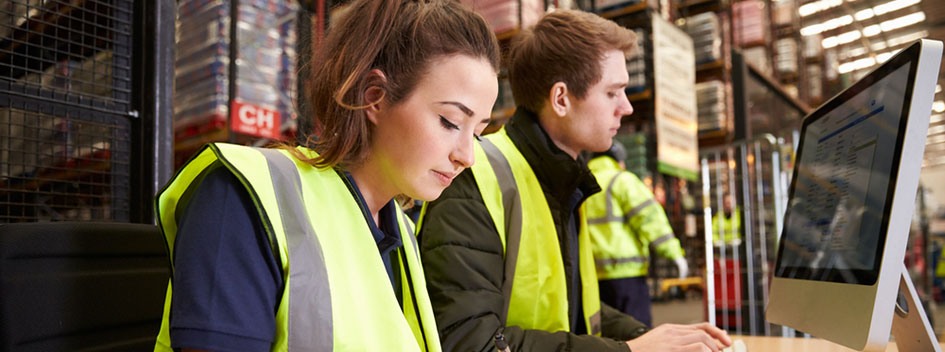
How Virtual Storeroom Management Transforms MRO
Gone are the days of manually managing inventory, tracking orders, and dealing with outdated stock. With virtual storeroom solutions, businesses can now handle their MRO needs more efficiently, cutting down on wasted time, resources, and money.
7 Ways Virtual Storeroom Management is Making MRO Easier
Here’s how virtual storerooms are simplifying MRO and helping you stay on top of your inventory game.
- Real-time inventory tracking
- Streamlined reordering
- Improved accuracy
- Increased efficiency
- Cost savings
- Predictive maintenance and data insights
- Flexibility and accessibility
1. Track inventory in real time.
One of the biggest advantages of virtual storeroom management is the real-time tracking of inventory. Instead of relying on periodic manual counts, these systems let you see exactly what’s in stock at any given moment. This helps reduce the chances of running out of critical supplies and improves ordering accuracy.
Tip: Automated systems can send alerts when stock is running low, so you can reorder before running out. This kind of visibility means less downtime and smoother operations overall.
DXP’s virtual storeroom solutions provide live inventory updates, so businesses never have to worry about unexpected shortages. Our system integrates with your supply chain to automatically reorder parts before they run out, ensuring smooth operations without delays.
2. Reorder with ease.
With virtual storeroom management, reordering becomes a breeze. The system keeps track of stock levels and automatically generates purchase orders when needed. This eliminates the guesswork and manual processes associated with ordering.
Having the ability to streamline reordering reduces overstock and ensures that you always have what you need on hand.
3. Enjoy better accuracy.
Manual data entry and inventory tracking are prone to human error. With virtual storeroom systems, you get precise and accurate data, reducing mistakes that could lead to overstocking or running out of critical items.
Tip: Barcodes, RFID tags, and other automation tools help ensure accurate inventory counts, reducing the likelihood of miscounts or data entry errors. In the long run, this means more reliable stock levels and fewer disruptions to your MRO operations.
Learn more about DXP’s MRO Integrated Supply Services.
4. Boost efficiency.
By digitizing storeroom management, employees spend less time tracking inventory and manually placing orders. Instead, they can focus on more important tasks. Virtual storerooms also improve workflow by reducing time wasted on searching for items, tracking down orders, or correcting stock errors.
Tip: Integrate your virtual storeroom with other systems like CMMS for seamless workflow and better efficiency.
At DXP, we specialize in making these integrations smooth and hassle-free. Our solutions not only enhance communication between systems but also reduce manual data entry errors. This means your team can focus more on getting the job done rather than managing inventory. With everything connected, you’ll experience improved response times to maintenance needs and a more efficient workflow overall.
Read this article to learn how DXP solves data challenges: Digitization of Data is Key to MRO Supply Chain Management.
5. Save on costs.
Virtual storeroom management can save money in the long run. You reduce waste by only ordering what you need, cut down on labor costs by automating time-consuming tasks, and prevent expensive downtime caused by running out of essential parts or tools.
With better control over your stock, you spend less on storage, avoid rush orders, and free up capital!
6. Gain predictive maintenance insights.
Virtual storerooms don’t just track inventory — they provide valuable data insights. These systems can show you usage patterns, allowing you to anticipate when you’ll need to restock certain items or plan for maintenance. When paired with predictive maintenance tools, you can avoid equipment failure by replacing parts before they wear out.
Here are some examples of valuable predictive maintenance insights:
- Wear and tear patterns
- Equipment usage trends
- Failure rate predictions
- Performance degradation
- Environmental factors
- Anomaly detection
- Lifecycle management
- Parts inventory needs
- Maintenance optimization
- Cost-benefit analysis
Here’s a tip: use the data from your virtual storeroom to plan ahead for large orders, seasonal fluctuations, or maintenance schedules.
With DXP’s supply chain services, clients benefit from real-time data tracking and customized reports that help them spot trends early. This helps businesses plan ahead, reduce downtime, and avoid costly surprises by ordering parts or scheduling maintenance before issues arise.
7. Access it flexibly.
Virtual storerooms offer the flexibility to manage inventory from anywhere. You can access stock levels, order history, and data analytics from any device with an internet connection. This level of accessibility makes managing MRO tasks simpler and more convenient, especially for businesses with multiple locations.
Ready to Modernize Your MRO Management?
If you’re ready to upgrade your MRO management, virtual storeroom solutions could be the answer. At DXP, we specialize in helping businesses streamline their MRO processes with modern technology. From inventory automation to predictive maintenance, we have the tools and expertise to take on your MRO management.
Contact DXP today to learn more about our virtual storeroom solutions.